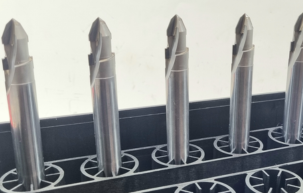
Advanced Polishing Techniques for Superior PCD Composite Performance
Unlocking the Potential of Polishing PCD Composites in Metallurgy
Polishing PCD (polycrystalline diamond) composites is a pivotal process in the metallurgy and mining sectors, particularly in the manufacturing of hard materials and alloys. Renowned for its exceptional hardness and thermal conductivity, PCD is a synthetic diamond material extensively used in cutting, grinding, and drilling applications. Polishing PCD composites not only enhances their surface finish but also significantly boosts their performance characteristics.
Benefits of Polishing PCD Composites
1. Surface Roughness Reduction
One of the primary advantages of polishing PCD composites is the reduction of surface roughness. A polished surface minimizes friction during operation, leading to increased efficiency and prolonged tool life. This is crucial in industries where precision and durability are paramount. Additionally, a smoother surface finish can reduce the accumulation of debris and wear particles, further extending the operational lifespan of tools and components made from PCD composites.
2. Enhanced Performance
The improved surface quality achieved through polishing translates directly into better performance. Polished PCD composites exhibit lower friction and wear, resulting in higher efficiency and longer-lasting tools. This is especially important in high-precision applications where consistent performance is essential.
Techniques for Polishing PCD Composites
1. Mechanical Polishing
Mechanical polishing involves the use of abrasive pads and slurries to achieve the desired surface finish. This method is effective for achieving a smooth surface but may not reach the ultra-smooth levels required for certain high-performance applications.
2. Chemical Mechanical Polishing (CMP)
CMP combines chemical and mechanical actions to remove material at a microscopic level. This technique produces an ultra-smooth surface, which is often necessary for applications demanding high precision and performance.
3. Abrasive Polishing
Abrasive polishing employs finer abrasives to achieve a polished finish. This method is essential for applications that require a high degree of precision, providing a smooth and refined surface.
Aesthetic and Functional Enhancements
1. Aesthetic Qualities
In addition to enhancing performance, polishing PCD composites plays a significant role in achieving specific aesthetic qualities. In applications such as jewelry making or high-end tooling, the appearance of the final product is as important as its functionality. Polished PCD composites can exhibit a glossy finish that elevates their visual appeal, making them more desirable for consumers and industries alike.
2. Coatings and Surface Treatments
The polishing process also facilitates the application of coatings or surface treatments. A well-polished surface ensures better adhesion of any subsequent coatings, further enhancing the material’s properties and performance. This is particularly relevant in industries where corrosion resistance or wear resistance is critical.
Conclusion
The importance of polishing PCD composites cannot be overstated in the metallurgy and mining sectors. The benefits of enhanced surface finish, improved performance, and aesthetic appeal make polishing an essential step in the manufacturing process. As the demand for high-quality materials continues to grow, understanding the intricacies of polishing PCD composites will empower professionals to make informed decisions that drive efficiency and innovation in their respective fields.
Polishing PCD composites is not just about achieving a smooth surface; it is about unlocking the full potential of these advanced materials to meet the demanding requirements of modern industrial applications.